OUR TECHNOLOGY
Advanced Technology for Superior Quality
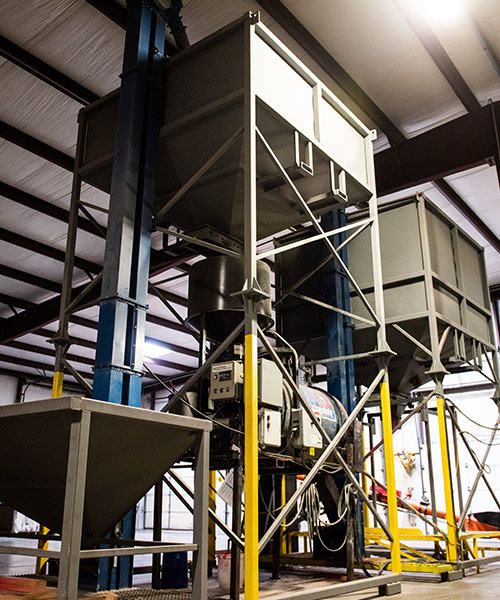
High Precision Seed Treating Equipment
Mid-State Seed operates a new and updated Gustafson RH2000 high precision seed treating system. The RH2000 utilizes a Mist-O-Matic® atomizer for improved treatment-to-seed coverage and does not require any lubrication. Equipped with a UL 508 Listed control panel that controls four pumps simultaneously or individually, this system also allows you a choice of treatments and/or fungicides. A 12″ color, touch screen HMI interface, highly accurate AC variable frequency drives and programmable logic controller automation (PLC), make this treatment technology easy to format to your specifications while ensuring accuracy.
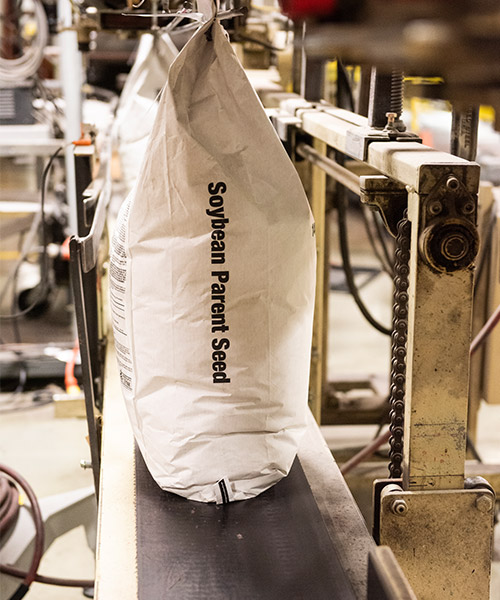
Advanced Automated Packaging
We measure your seed as precisely as we clean it. Our fully automated bagging equipment packages the final product to your request: in bags coded with the variety, test date and number of seeds per pound. The Inglett Model 8800 GV Duplex Bagging Scales and automated Model 3500 Bag Hanging System guarantee each bag to be within 0.2 of a pound of its labeled weight. Bagged product is then delivered to our Fischbein Bag Closing Systems and coded with our Fox Jet Ink Printing System. Bags are palletized with our automated Chantland Palletizing System followed by an automated Kauffman Pallet Stretch Wrapping System.
Our semi automated bulk bag Detecto/Cardinal Loading System for tote bags and our automated Thompson Scale for loading center flow discharge tote boxes also deliver the precision accuracy we set for all of our customers.
Mid-State Seed delivers its quality product by the bag, bulk bag and boxes. Finished products are then shipped or stored to your specifications.
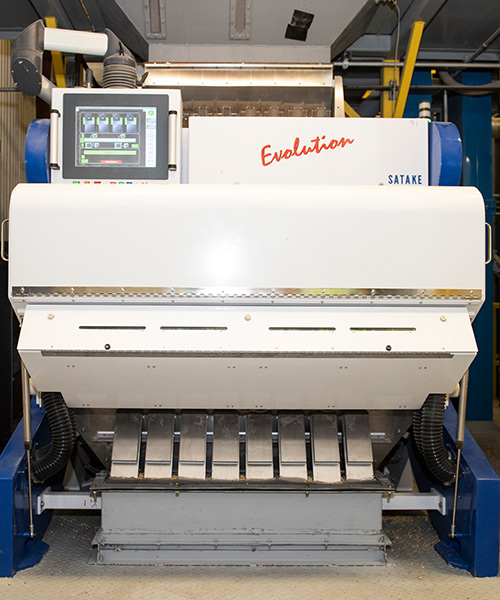
Satake Evolution RGB And Shape Sorter
Our Satake color and shape sorters are what set Mid-State Seed apart from other packaging facilities. These machines use pixelated images to recognize and sort out any unwanted grain, moldy, diseased, stained, and misshaped seed as they are being processed through our conditioning system. They also have the ability to hone in on a particular off type hilum with a few simple adjustments by our trained tower operators. The ejectors release a short burst of air and the unwanted object is then discarded from the rest of the product. Having this technology allows Mid-State Seed to not only efficiently provide the finest quality of seed, but also improves the visual appearance of the final product.
Innovative Bin Management System
Mid-State Seed has invested in the latest technology to provide precision production, cleaning and handling of soybeans and other small grains. Grain shipments are unloaded at our facility, avoiding inclement weather, and stored in our bulk storage tanks. This sophisticated bin management system alerts operators to adjust the controls for optimal temperature and moisture. Grain and seed are then gently sent to and throughout our processing facility with great care by way of our advanced handling equipment.
Carter Day Aspiration Technology
From our storage systems, grain is first taken to our pre-cleaning, 24″ x 56″ Carter Day Scalperator which features scalping, rescalping and aspiration in a single machine to provide a high capacity method for removing roughage, light fines and chaff in a single pass. This process eliminates unwanted waste in the pre-cleaning stage and allows more bulk to move through our other systems. Ultimately, this increases the production of our Cimbria Delta 108 Air Screen Cleaner.
Comprehensive Inventory Management System
Mid-State Seed uses the AGRIS V9 Comprehensive Business Management System developed by John Deere. Its professional programming and strong support system provide our customers and growers with the precise accuracy required.
Cimbria Delta Super 108 Cleaner
The Cimbria Delta Super 108 uses a combination of two scalping and six sifting screen rows for roughly 24 square meters of screen cleaning. Electronic adjustments for feeder and bottom fans, and manual adjustments for precision air control allow our operators to maintain a consistent product flow with minimal (if any) damage to the seed. The machine’s efficient shoe shake system, with its accurately matched stroke and frequency, is complemented by Cimbria’s highly developed pre- and post-suction system. Two airlifting blowers at the bottom of the machine ensure unrivaled air cleaning and grading. Quality control continues with our multistage separation process, which includes a spiral separator that uses an 18-core system to remove undesirable impurities from the product.
Oliver Maxi-Cap and Hi-Cap Gravity Separators
After the seed travels through the spiral separator, it is conveyed to an Oliver Maxi-Cap 4800 gravity table with 90 square feet of deck, which gives our seed a high quality separation at high capacity. Particles of similar size are separated at different and specific densities by stratifying the product. At the end of this separation, we have a 12- to 18-inch cut off on the lower side of the gravity deck where a mix of quality seed and marginal seed is collected. This collection of product is sent to an Oliver Hi-Cap 240 gravity table, where it is stratified again for a more precise separation of the higher quality seed from the marginal seed. The higher quality seed from this separation is blended back into our flow from the 4800 while the marginal seed is discarded.